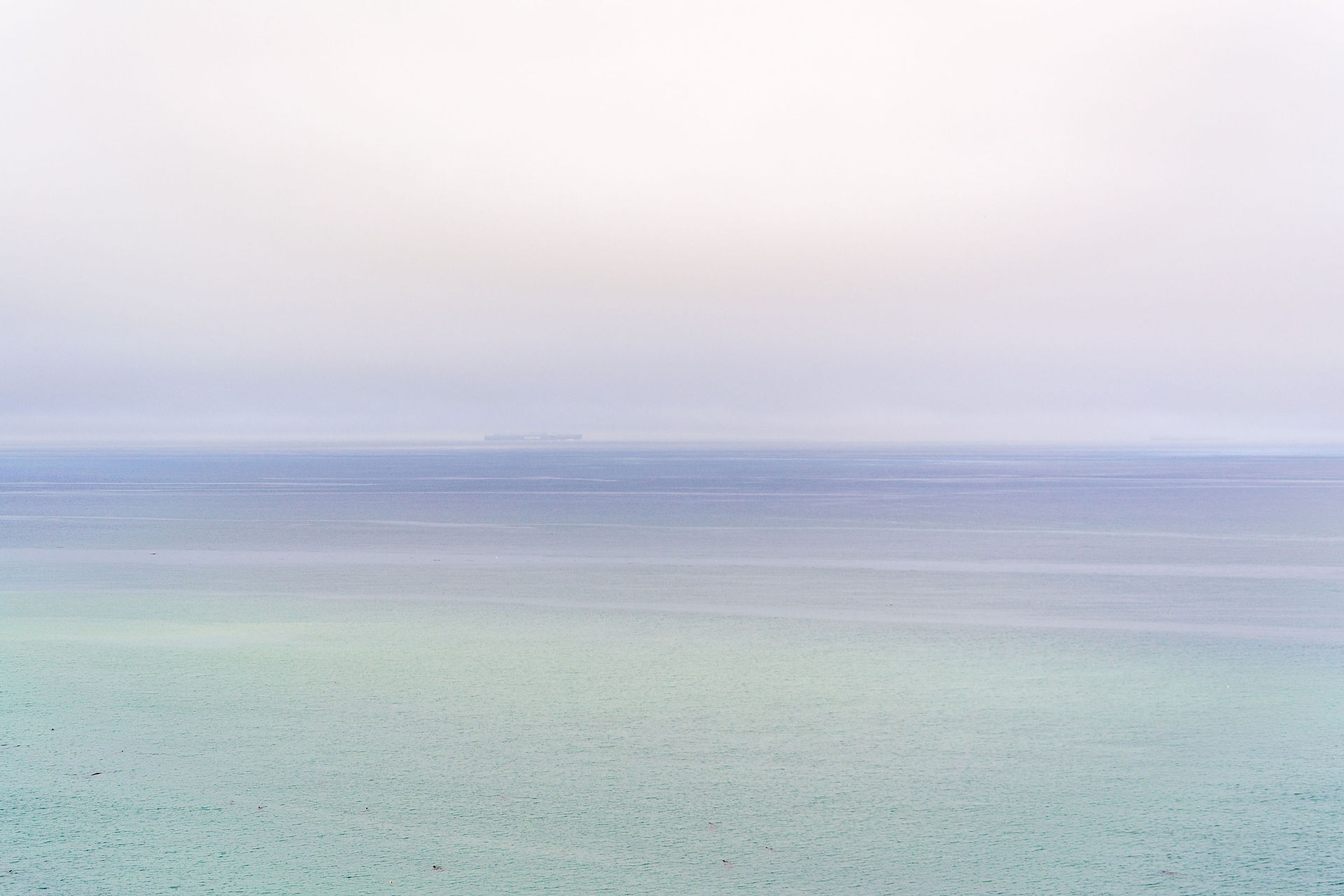



What is the process?
A majority of plastic bags are made out of polyethylene (a petroleum-derived polymer). The manufacturing process that is used to make plastic bags is called Blown film extrusion. First, polyethylene beads are deposited into a heated barrel, which contains a screw. The screw will begin to motor around and the beads will be pushed through the barrel as they melt into the desired state. The barrel contains high levels of heat, pressure, and friction which help contribute to the melting of the beads. A screen pack is at the end of the barrel which help get rid of the unwanted contaminants. After, the molten polymer is passed into the dye, which is an upward cylinder. Above the dye there are two nip rolls and are used to pull the plastic up. The thickness of the bag depends on the the speed of pulling. An air ring is put outside the dye and its main purpose is to cool the plastic. The next step is to blow a bubble. A nozzle is located in the center and it blows air into the bag creating a bubble this creates the ratio of the new size. Lastly, the nip rolls compresses the bag back into a double-walled film and the film is stored to cool. Once it’s cooled, it can be processed into bags with colors, logos, and even add handles.